Project Logistik Center Rheinland
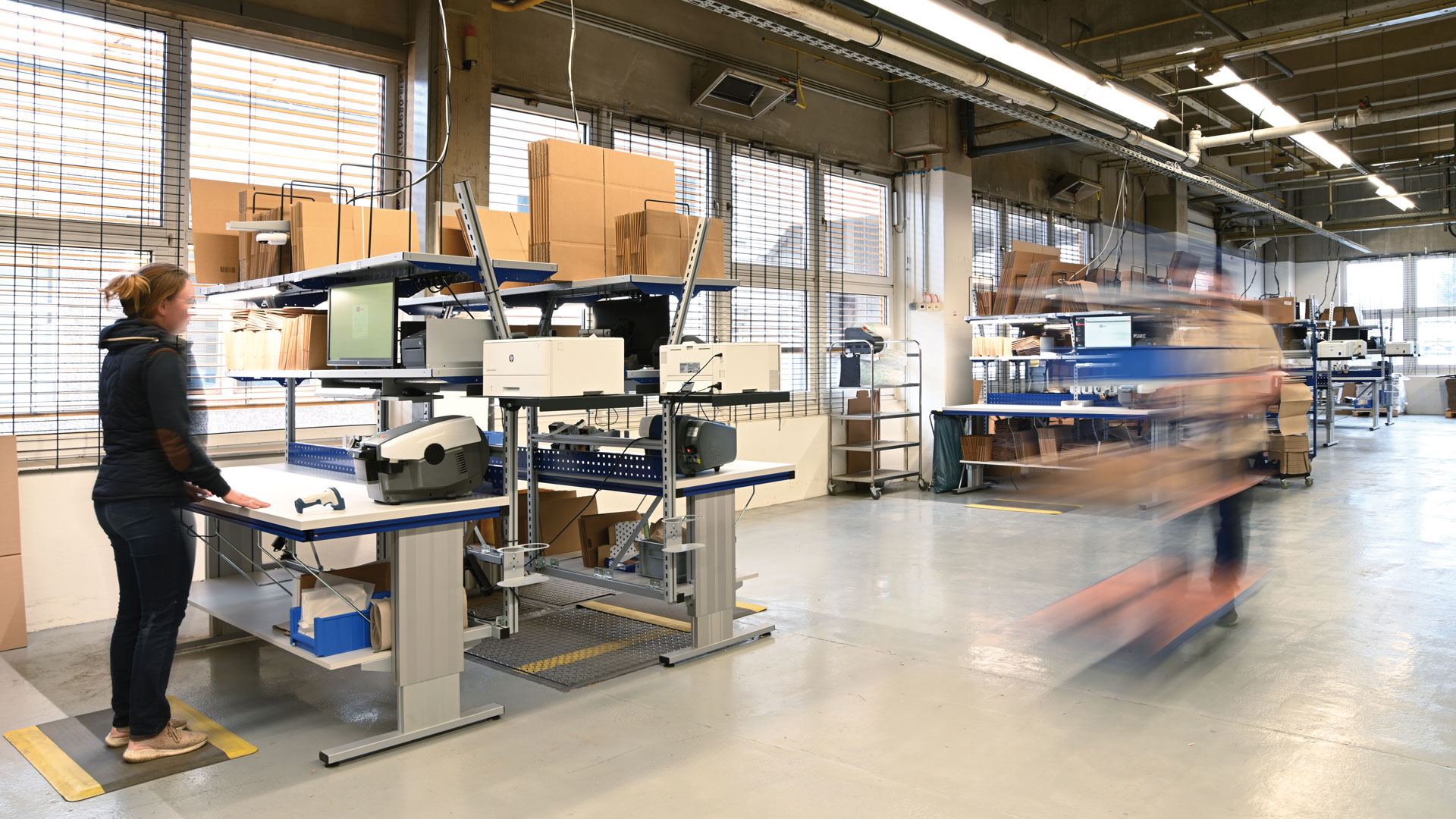
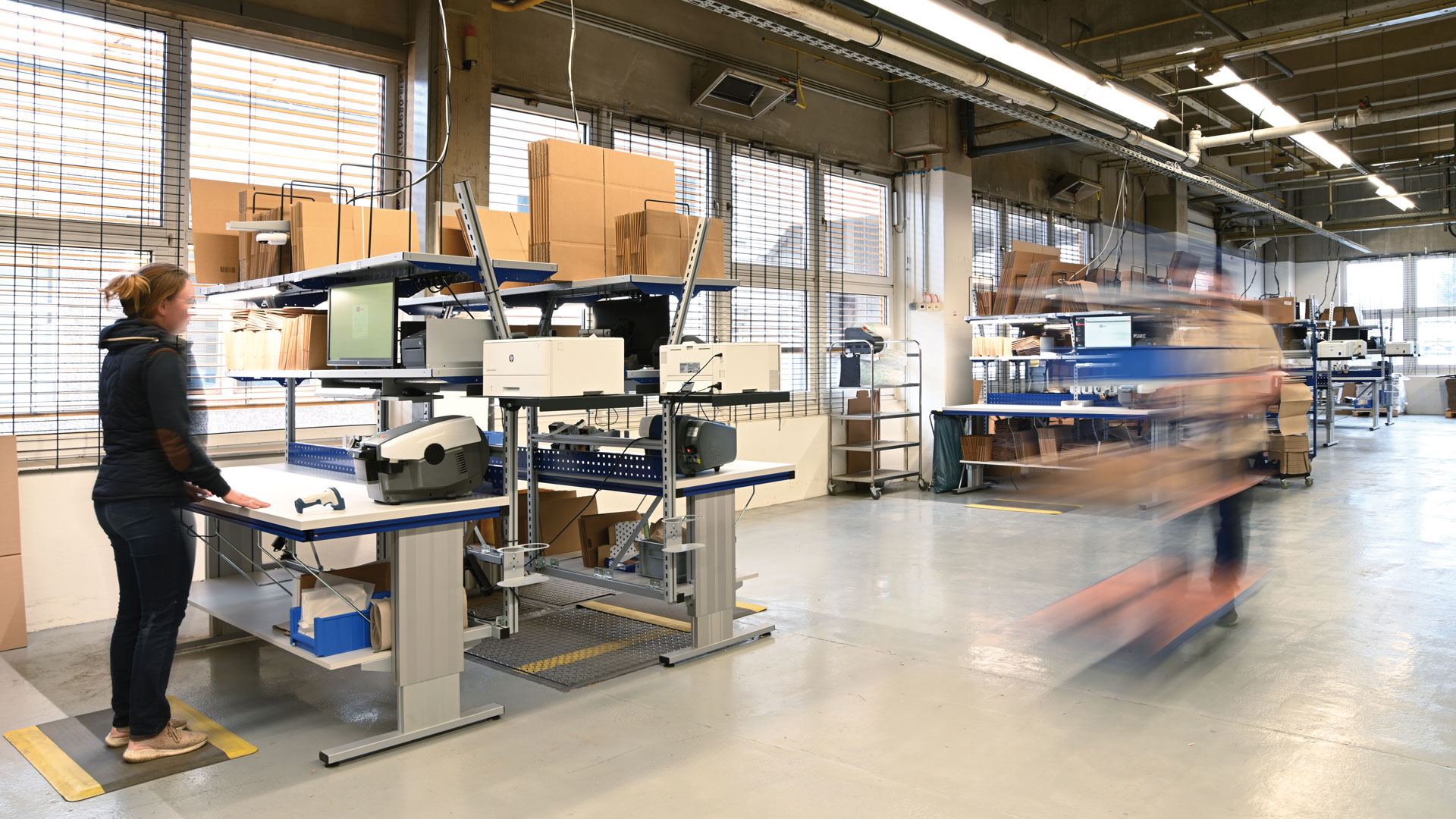
The fulfilment service provider Logistik Center Rheinland OHG from Rheinbach handles the storage, packing, packaging and delivery of goods for its customers. To ensure that the requirements of various customers can be perfectly met, the packing stations were rethought by our sales partner BB-Verpackungen GmbH. A comprehensive inventory was carried out:
Analysing the spatial conditions, packaging processes and required work equipment, from hand dispensers and boxes to cameras for video documentation, formed the starting point for targeted improvements to the packing stations. "Optimum processes at the packing stations are the be-all and end-all, particularly in fulfilment, and thus ensure the necessary efficiency and flexibility to meet all customer requirements, especially during Black Week or Christmas sales," explains the Managing Director of Logistik Center Rheinland.
The 20 new electrically height-adjustable SYSTEM FLEX packing tables enable individualised loading with the work equipment required by each customer. Thanks to storage surfaces above and below the table top, the work surface has been reduced by almost 50%. This enabled new workstations to be created that make optimum use of the available space. The upper shelves are optimised for easy access thanks to 20° inclined HR add-on profiles and offer space for lots of accessories: various cardboard boxes, a barcode scanner, a laser printer and a label printer, a camera, a mini PC as well as a monitor and a keyboard with mouse are practically integrated. Several manual dispensers - with adhesive tapes printed in different colours depending on the customer - and/or a wet gluing machine are planned at a fixed location. The packaging process is standardised as far as possible and leads to a higher throughput and minimisation of the error rate. The SYSTEM FLEX packing tables have not only increased efficiency, but have also created a modern, ergonomic and adaptable working environment for the customer's employees.
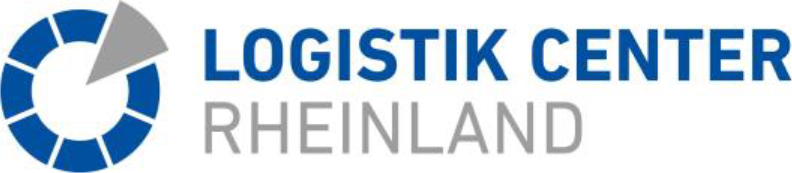

Logistik Center Rheinland OHG

Logistik Center Rheinland OHG
Industriestraße 7
D-53359 Rheinbach

20 Workstations set up

SYSTEM FLEX electrically height-adjustable packing tables with intermediate shelf and dividers for cardboard boxes under table
Shelves with keyboard pull-out
Universal side trays for delivery note printers
Customised camera mount adapted to the customer

Sales partner
BB-Verpackungen GmbH
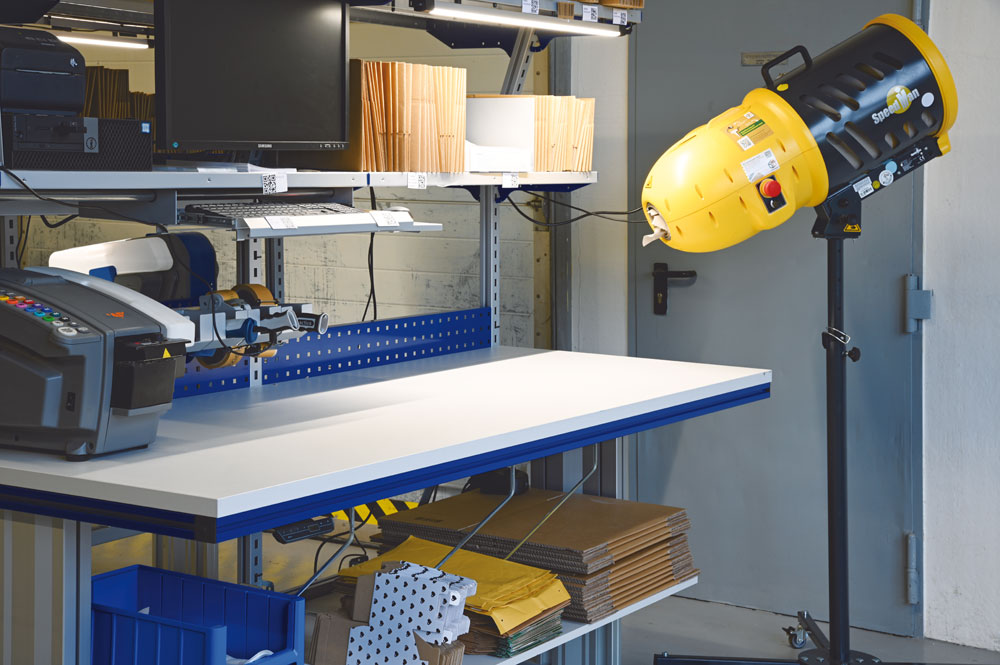
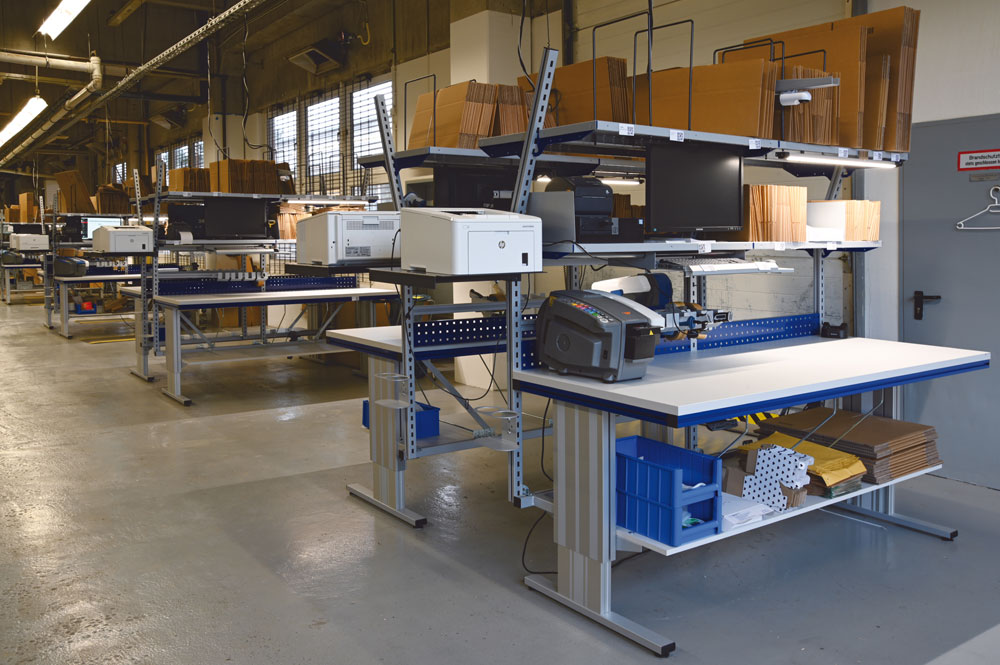
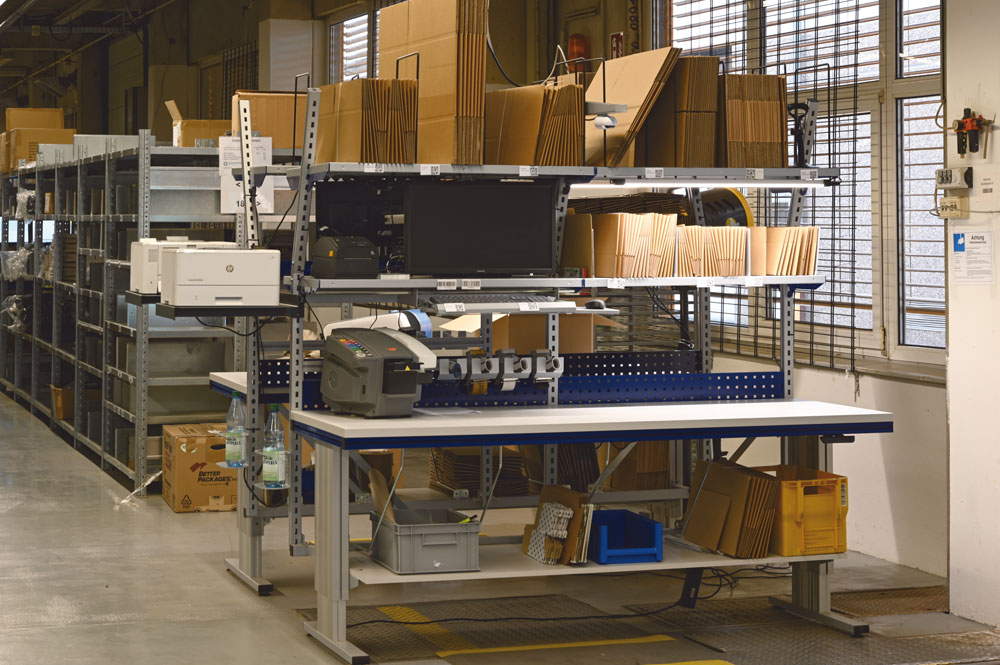
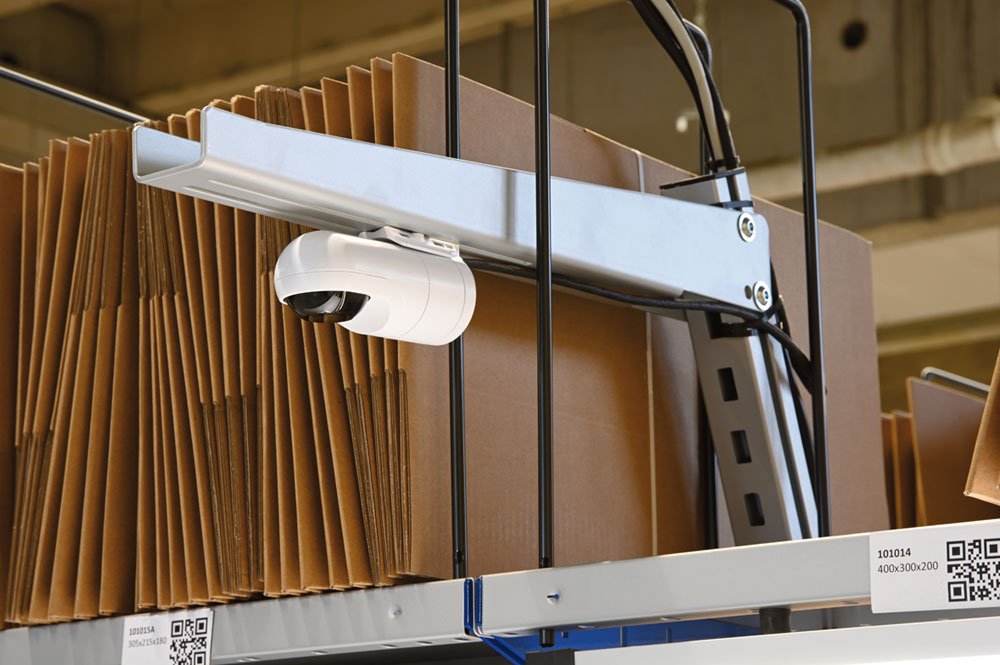
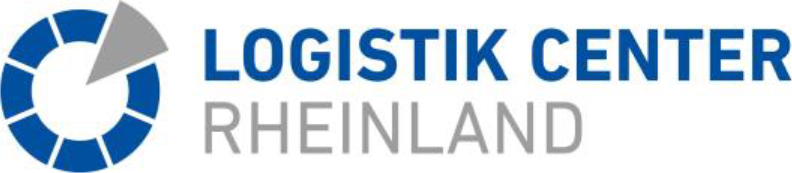

Logistik Center Rheinland OHG

Logistik Center Rheinland OHG
Industriestraße 7
D-53359 Rheinbach

20 Workstations set up

SYSTEM FLEX electrically height-adjustable packing tables with intermediate shelf and dividers for cardboard boxes under table
Shelves with keyboard pull-out
Universal side trays for delivery note printers
Customised camera mount adapted to the customer

Sales partner
BB-Verpackungen GmbH
The fulfilment service provider Logistik Center Rheinland OHG from Rheinbach handles the storage, packing, packaging and delivery of goods for its customers. To ensure that the requirements of various customers can be perfectly met, the packing stations were rethought by our sales partner BB-Verpackungen GmbH. A comprehensive inventory was carried out:
Analysing the spatial conditions, packaging processes and required work equipment, from hand dispensers and boxes to cameras for video documentation, formed the starting point for targeted improvements to the packing stations. "Optimum processes at the packing stations are the be-all and end-all, particularly in fulfilment, and thus ensure the necessary efficiency and flexibility to meet all customer requirements, especially during Black Week or Christmas sales," explains the Managing Director of Logistik Center Rheinland.
The 20 new electrically height-adjustable SYSTEM FLEX packing tables enable individualised loading with the work equipment required by each customer. Thanks to storage surfaces above and below the table top, the work surface has been reduced by almost 50%. This enabled new workstations to be created that make optimum use of the available space. The upper shelves are optimised for easy access thanks to 20° inclined HR add-on profiles and offer space for lots of accessories: various cardboard boxes, a barcode scanner, a laser printer and a label printer, a camera, a mini PC as well as a monitor and a keyboard with mouse are practically integrated. Several manual dispensers - with adhesive tapes printed in different colours depending on the customer - and/or a wet gluing machine are planned at a fixed location. The packaging process is standardised as far as possible and leads to a higher throughput and minimisation of the error rate. The SYSTEM FLEX packing tables have not only increased efficiency, but have also created a modern, ergonomic and adaptable working environment for the customer's employees.
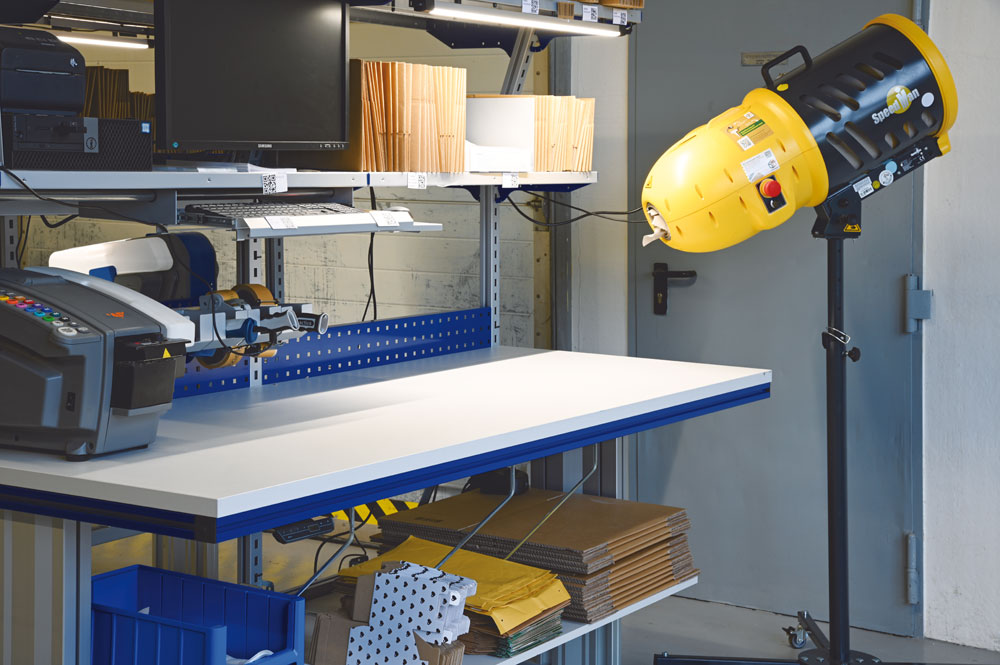
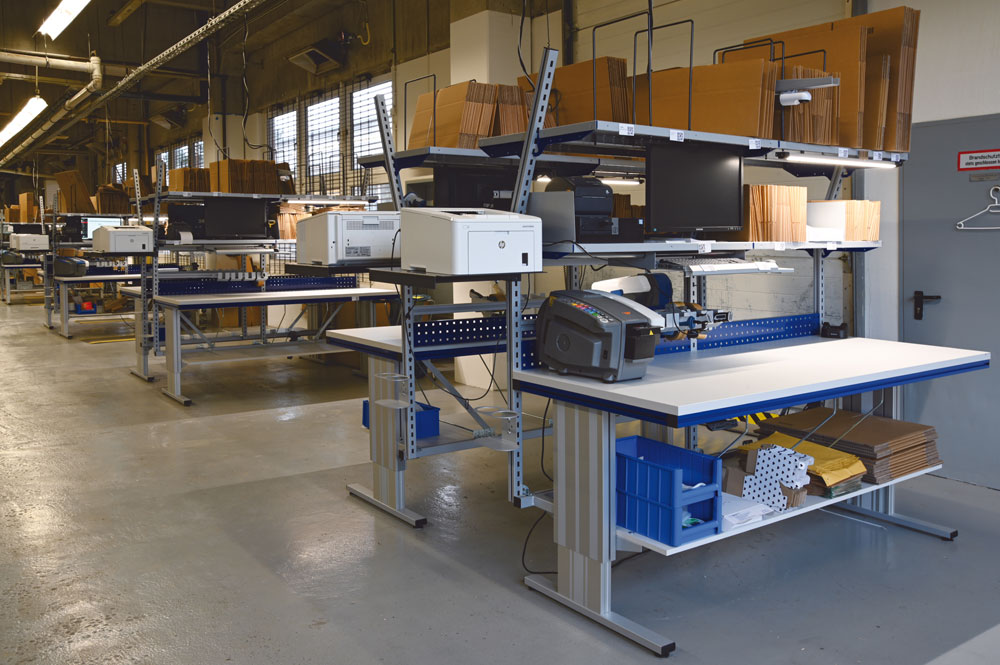
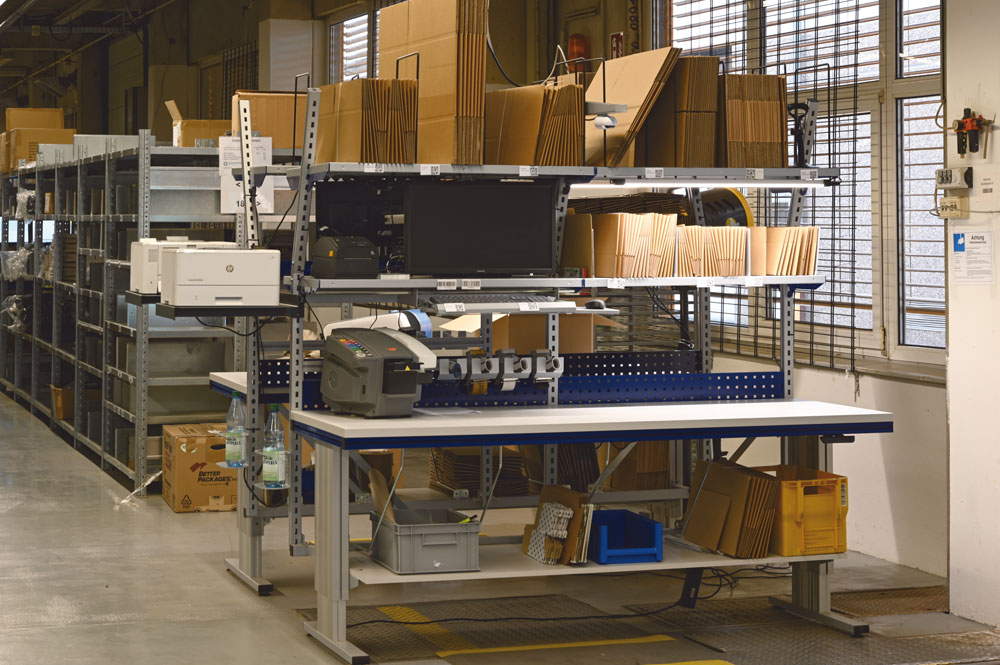
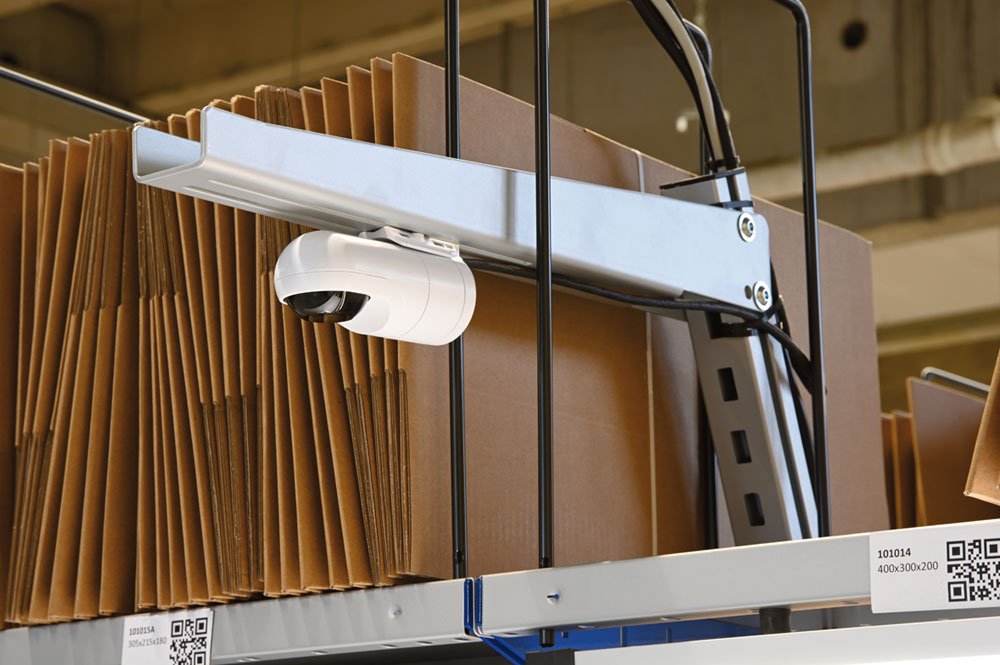