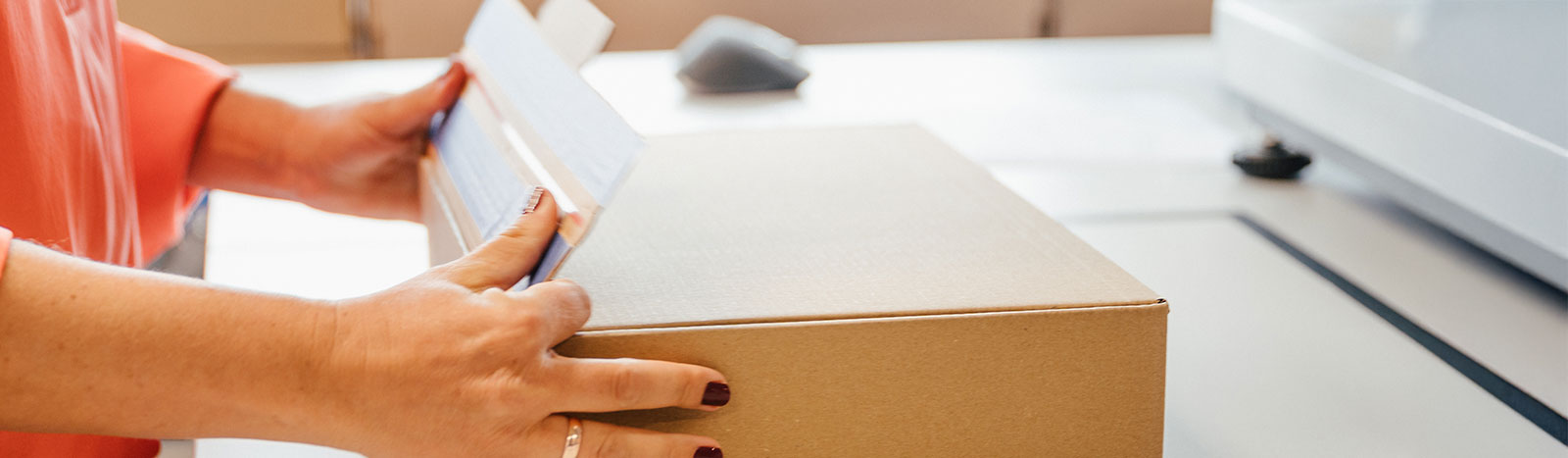
How to optimise your packaging process
Info
Companies can benefit from this by optimising the packaging process. This not only ensures greater efficiency, but also saves costs and protects the environment if products can be packaged sustainably. In this article, you will learn how you can optimise your packaging process and make it more efficient. Rocholz provides you with specific measures to do this.
Increased efficiency through automation and time savings
Automation plays a central role in optimising the packaging process. The use of packaging machines can significantly reduce the time required and minimise errors.
Rocholz has also developed flexible solutions for this that can be integrated directly into our SYSTEM FLEX packing tables. These include our ProtecTable products, for example, which combine a lift, a platform and a silo to promote ergonomic working and optimise the packaging process.
Our products are also designed so that paper padding machines can be integrated easily and in a space-saving manner. Ergonomic work processes are well thought out and taken into account in the design of gripping areas.
Ergonomic machine integration for effortless packaging
A decisive step towards optimising your packaging process is the ergonomic integration of machines directly at the workstation. At Rocholz, we offer you the option of integrating your paper padding machines into your packing tables in a space-saving and ergonomic way. Discover our highly functional packing tables, which have been developed to optimise workflows.
Our SYSTEM FLEX basic tables are available in two versions:
- Manually adjustable: With a width of 1,200, 1,600 or 2,000 mm, depth of 800 mm, and infinitely height-adjustable from 690 to 960 mm. These tables offer a cut-out for material ejection and a maximum surface load of 300 kg.
- Electrically adjustable: This version is also available in a width of 1,200, 1,600 or 2,000 mm, 800 mm deep and offers electric, infinitely variable height adjustment from 720 to 1,120 mm. With a lifting speed of 12 mm/sec, this table also has a maximum surface load of 300 kg.
We also offer various accessory packages. Of course, the tables can be customised with additional accessories from the System Flex range.
Visit our showroom and see for yourself the ergonomic solutions that optimise your packaging process effortlessly.
Time saving thanks to sophisticated design
Another important aspect is the design of the packaging, which can be ideally customised to the corresponding product. Forward-looking packaging is designed in such a way that it is ready for use in just a few simple steps. This not only saves time, but also reduces material consumption.
One example of how packaging can be optimised is automatic bottom cartons or cartons with integrated closures. These require less adhesive tape and are quicker to seal, which increases efficiency.
The following short film shows you what integrated volume optimisation can look like at a packing workstation. Our iPackAssist is a combination of SYSTEM FLEX with several assistance systems. The system provides the ideal basis for efficiently organising packaging processes in just a few steps:
Optimum supply of the packing stations
A well-designed packaging process also includes optimising the supply to the packing stations. Materials such as air cushions or paper pads, which are produced directly at the packing station, save time. Employees do not have to run to the warehouse all the time.
This decentralised material provision increases efficiency and ensures a smooth workflow. Our ProtecTable provides an optimum basis for the design of packing stations.
Ergonomic workplace design
Ergonomics in the workplace influences the efficiency and well-being of employees. The packaging process can therefore be optimised through the use of ergonomic technologies. Height-adjustable packing tables and lifting systems are examples of ergonomic solutions that improve working conditions.
Ergonomically designed workstations reduce the risk of health problems and increase productivity. At Rocholz, we offer customisable solutions that can be optimally integrated into the material flow. They fulfil the requirements of employees.
Ergonomic adjustments at the workplace
Height-adjustable packing tables allow employees to work in a comfortable position (including standing). This reduces the risk of muscular and skeletal disorders.
Our movement and process analyses provide extensive data and findings on the basis of which the workplace is designed ergonomically and efficiently. Real-time analysis with modern sensor technology makes it possible to detect stress at an early stage and at the same time to create recommendations for action in order to optimise movement sequences with a view to health. See for yourself:
However, ergonomic workstations not only have health benefits. They help to optimise the packaging process and also increase productivity. Employees who work in a pleasant environment are less prone to absenteeism. They also work more efficiently. If the packaging process is optimised, this leads to a higher production rate and lower costs.
Quality control and error prevention
Quality control is an important aspect in optimising the packaging process. Image-based assistance systems such as InspecTable enable reliable detection of deviations and errors. These systems analyse both the packaging and the contents and compare them with predefined target conditions. This enables errors to be recognised and avoided at an early stage.
In addition to quality control, error prevention techniques play an important role. Mechanical or electronic devices ensure that packaging errors either do not occur in the first place or are recognised immediately.
Continuous improvement and zero-defect strategy
A continuous improvement process (CIP) and a zero-defect strategy help to ensure the quality of the packaging in the long term. Weak points are identified and eliminated through regular checks and adjustments to processes.
Optimising the packaging process in this way leads to a constant improvement in quality and reduces the complaint rate.
Documentation and traceability
Complete documentation and traceability of the packaging processes ensure transparency and help to analyse errors. Digital documentation systems such as DocumenTable make it easy to record and store packaging data.
The integration of these systems into existing IT structures ensures seamless data transfer and facilitates tracking.
With DocumenTable, photos and videos of the parcel contents can be saved together with relevant information such as delivery note number and time stamp. This ensures clear allocation of the data and facilitates tracking.
The data is stored on an integrated memory and can be accessed via the network.
Digital documentation offers the advantage that all packaging steps are transparent and traceable. This not only makes it easier to analyse errors, but also to communicate with customers and partners.
In the event of complaints, it is possible to quickly identify which packaging step was faulty. This shortens the processing time and increases customer satisfaction.
Cost and space savings for packaging
A well-planned packaging process also helps to reduce costs and save space. Standardisation of load unit sizes is an important factor here.
If the packaging sizes are limited to a few variants, this saves space and time during selection and storage. Height-adjustable cartons are also an interesting solution for optimising the packaging process, as they can be easily adapted to different product sizes.
Checking the packaging stock
Efficient control of packaging stock is crucial to avoid shortages as well as excess stock. A good supplier of packaging materials should offer flexible delivery times in order to provide the required material quickly. This frees up valuable storage space and allows production to continue smoothly.
Integration and adaptation to existing systems
Seamless integration of new processes and systems into existing workflows is essential if you want to optimise a packaging process. Flexibility is required in order to be able to take various requirements and circumstances into account.
Our SYSTEM FLEX packing table is ideal for all employees who value freedom and flexibility as well as customisable ergonomics.
Sustainability and environmental aspects
Environmentally friendly packaging materials and sustainable practices are another important aspect of optimising the packaging process. Choosing recyclable or biodegradable materials can significantly reduce the environmental impact.
The new EU regulations aim to make packaging subject to stricter recycling requirements and set minimum targets for the proportion of recycled material in plastic packaging.
Strategies to reduce waste, such as the use of reusable packaging or the optimisation of packaging sizes - for example by limiting the proportion of empty space to a maximum of 50% - also contribute to sustainability. Recycling programmes for packaging materials help to conserve resources and minimise waste.
From 2030, certain single-use plastic packaging will be banned, which should further reduce the amount of waste. Consumers will also be given more opportunities to reuse and refill packaging in order to promote the circular economy.
Optimisation of the gripping area
A well-organised reach space is crucial for efficiency in the workplace. At Rocholz, we offer an extensive range of accessories that ensure that the work surface always remains free. Clever holders and storage systems ensure that all required materials are always within easy reach and clearly organised. This reduces search times and enables a smoother workflow.
Economic consideration
A cost-benefit analysis of process optimisation shows what savings potential there is and how quickly investments pay for themselves. Long-term economic benefits, such as lower operating costs and greater efficiency, make optimising the packaging process a worthwhile investment.