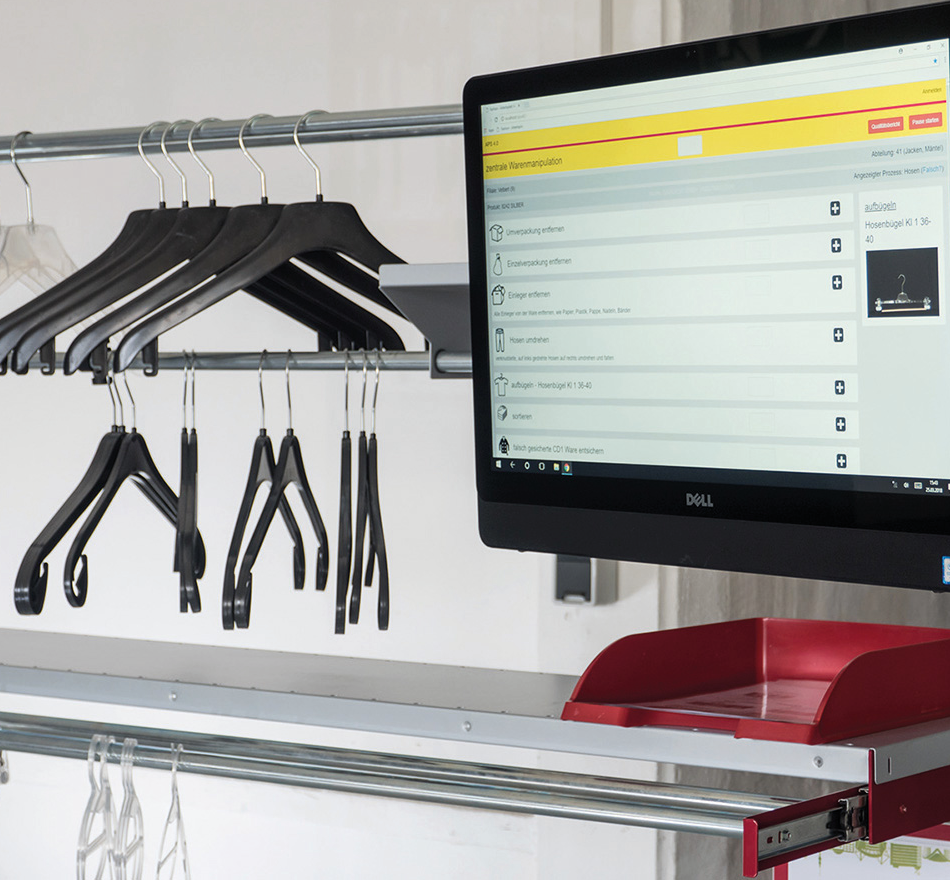
4 tips to optimise your order picking
Tips
Picking is one of the most critical processes in logistics and offers considerable potential for reducing costs and improving performance. Efficient and effective order picking with high throughput and a high level of accuracy is therefore a must for any successful company that wants to improve its output performance.
Whether you work for a small, medium-sized or large company, the constant optimisation of order picking is crucial in order to remain competitive and increase sales.
Rocholz would therefore like to give you 4 tips on how you can effectively optimise your order picking. We are a company with over 100 years of tradition and a wealth of experience. Rocholz offers you logistics workstations such as the SYSTEM FLEX, which not only have a far-reaching effect on work quality, ergonomics and efficiency. Our assistance systems, with which you can optimise order picking even better, can be ideally integrated into our logistics workstations.
Tip 1: Simplify complex tasks
The task of optimising order picking begins with the simplification of complex work processes. With the shift towards customised products and services, complexity is increasing in almost all sectors.
Tasks that were once quite simple and straightforward can now involve a multitude of steps, requirements and variables that make picking a challenging job. It is important that you utilise methods and tools that enable your team to effectively manage this increasing complexity.
To reduce complexity and optimise order picking, you should try to standardise and automate your workflows wherever possible and practical. This creates a standardised approach and allows your employees to focus on specific tasks to make the best use of their skills and expertise.
You can also use technology to support and facilitate the tasks of your employees so that you can optimise order picking. One such tool is our assistance system Simple Assist. Simple Assist is a ‘Plug & Produce’ system that supports complex tasks with simple visual instructions. The system's internal projector displays the work steps directly on the work surface, which guides employees in their activities. New employees can thus be familiarised more quickly. Even language barriers need not be an obstacle to familiarisation and work execution. This allows you to optimise the quality and efficiency of your order picking, even with increasing complexity.
Definition: Plug & Produce
Plug & Produce is a term used in automation technology. It means that devices or systems can be integrated into an existing system without the need for extensive configuration. The devices can simply be connected (plugged in) and put into operation.
Remember:
Simplifying complex tasks is an important first step in making your order picking more efficient. Technologies such as our Simple Assist can support you in this.
Tip 2: Use digital assistants for support
Using digital assistants is another effective way to optimise your order picking. In the modern working world, digital assistants simplify complex processes by providing employees with precise instructions and an overview of their work activities. They help to reduce errors, increase productivity and ensure a smoother workflow.
A digital assistant can be seen as a virtual colleague who supports your employees in their daily work. It helps them to concentrate on their main tasks and supports them in completing jobs more efficiently and effectively. With the right management system, several orders can even be completed at the same time. This is an important basis for batch picking.
A digital assistant can be very valuable when it comes to (multi-stage) order picking, where errors can cause high costs and reduce work efficiency. Our AssisTable assistance system is an excellent example of such a digital helper. AssisTable is a digital work catalogue that supports employees in picking and packing processes and thus helps to optimise order picking.
Expert tip:
When implementing digital assistants, it is important to consider the specific needs and processes of your organisation. A well-implemented digital assistant should be smoothly integrated into your existing processes and support your employees in their work instead of causing additional effort.
Remember:
Digital assistants can provide valuable support in efficient order picking. They help to improve work processes and contribute to error reduction, allowing you to successfully optimise your order picking.
Tip 3: Rely on quality assurance measures
Quality assurance is an integral part of any efficient picking system. The use of innovative technologies can help to detect errors and deviations early and reliably - before the goods reach the customer. This helps to maintain your company's good reputation, minimise losses and maximise customer satisfaction.
The use of quality assurance measures generally includes:
- Identification of potential sources of error
- Procedures for error prevention
- Measures for the early detection of errors
- Carrying out regular quality checks
Measures like these should be a priority in every company so that order picking can be sustainably optimised.
Our InspecTable system is an effective tool for this task. InspecTable is an image-based system that reliably recognises deviations and errors at an early stage by comparing them with the trained target situations. It can analyse individual items and their location or position, but can also show an overall picture. This allows you to ensure that your goods are correctly picked and packed before they leave your premises.
Expert tip:
Make sure that you regularly review and update your quality assurance measures. The use of modern technologies such as InspecTable can help to recognise errors at an early stage and avoid costly rework.
Remember:
Quality assurance measures are an essential part of optimising order picking. They help to minimise errors, increase efficiency and improve customer satisfaction.
Tip 4: Document your processes
Documenting your picking processes is another important step in optimising your picking. Accurate and complete documentation not only helps you to understand and improve your processes, but it can also help to reduce errors, facilitate the training of new employees and ensure compliance with regulations.
In addition, good documentation can also be a valuable resource when it comes to increasing the efficiency and productivity of your employees. It allows your employees to quickly access the information they need to do their jobs effectively. It can also help avoid misunderstandings and communication gaps that can lead to errors and delays.
Our DocumenTable assistance system can help you to document your picking processes effectively. With DocumenTable, you can easily create photos for documentation directly at the logistics workstation in the dispatch or goods receipt area. This complete documentation of the parcel contents helps you to understand and resolve any ambiguities or problems. With the support of DocumenTable, you can easily optimise your order picking.
Remember:
Complete documentation of your processes is an important step towards optimising your order picking. It helps to improve processes, minimise errors and increase efficiency.
Optimise your order picking with Rocholz
The regular optimisation of your order picking is crucial in order to remain competitive and continuously increase sales. By simplifying complex tasks, using digital assistants, implementing solid quality assurance and accurately documenting processes, you can optimise your order picking work steps and make them more efficient.
The assistance systems from Rocholz - Simple Assist, AssisTable, InspecTable and DocumenTable - are designed to help you with precisely these aspects. Our experts will be happy to assist you if you have any further questions about the products.