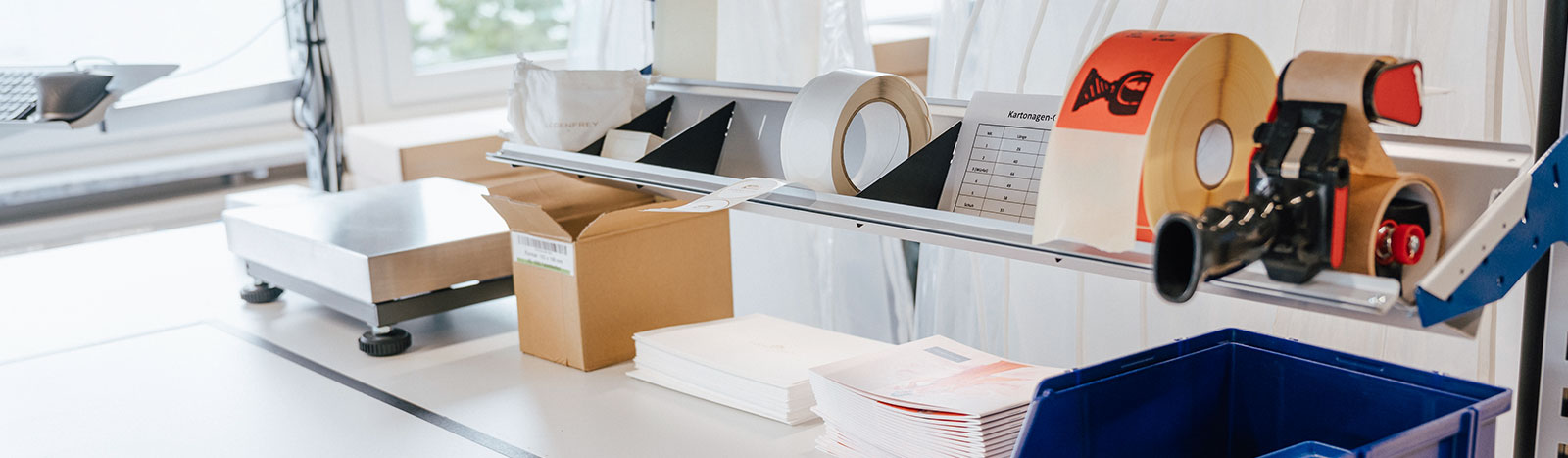
How to increase production with workplace optimisation
Info
The optimisation of workstations in production is crucial. It helps to ensure efficiency, quality and employee health. Companies are faced with the challenge of designing workstations in such a way that they are both ergonomic and functional. A well-planned workplace design helps to reduce absenteeism. It increases productivity. In this article, you will find out which measures contribute to workplace optimisation in your production and how you can implement them successfully.
Ergonomics in the workplace
Ergonomic design plays a central role in workplace optimisation in production. Height-adjustable workstations and ergonomic chairs ensure that employees can alternate between sitting and standing.
The right lighting is just as important. LED industrial luminaires with a colour temperature of around 4000 K ensure a pleasant working environment. Temperature fluctuations and noise should also be controlled in order to maintain employees' ability to concentrate.
Height-adjustable workstations
Height-adjustable workstations allow employees to change their position while working. This allows them to work both sitting and standing. This reduces the strain on certain muscle groups and improves blood circulation.
The advantage of electric height adjustment for ergonomic workstations is that the adjustment can be made quickly and easily. This is particularly important for shift work where different employees use the same workstation.
Standing workstations from Rocholz
Rocholz standing workstation systems are ideal for workstation design in production and offer high quality. They allow the desk height to be customised and therefore offer an ergonomic working environment.
Ergonomic task chairs
Ergonomic task chairs support dynamic sitting and therefore offer positive effects. They enable synchronised movement of the seat and backrest. A slight forward tilt of the seat and the option to customise the backrest help to achieve an optimal working posture.
Such chairs are also equipped with braked castors. These ensure mobility without any safety risks. An ergonomic task chair is also resistant to lubricants and cleaning agents. This increases its durability.
Optimum lighting
Lighting should be glare- and flicker-free to optimise the workplace in production. LED lighting with a colour temperature of around 4000 K promotes concentration and reduces eye fatigue.
Avoid multiple shadows. Ensure uniform illumination of the work area. The light colour can also be adjusted to support employees' biorhythms. Cool white light has a stimulating effect, while warm white light has a calming effect.
Are you interested in ergonomically designed workstations in logistics?
Environmental factors
In addition to lighting, temperature, noise and air quality also play an important role. A controlled room temperature prevents employees from overheating or overcooling.
Noise protection measures such as sound insulation or low-noise machines reduce stress and promote concentration. Good ventilation ensures a sufficient supply of oxygen and improves the air quality in the workplace.
Note: Good ergonomic design and optimised environmental factors are crucial for the health and satisfaction of employees.
Technological support and digitalisation
Assistance systems such as SimpleAssist and AssisTable offer considerable advantages. They guide employees through complex tasks using visual instructions and reduce errors. These systems are intuitive to use and do not require extensive IT knowledge.
Automation and robotics increase efficiency and improve the quality of work processes as part of workplace optimisation in production. These technologies take the pressure off employees. They enable them to concentrate on more demanding tasks.
Digital assistance systems
Digital assistance systems support employees in carrying out complex and varied tasks. Systems such as SimpleAssist project work steps directly onto the work surface and guide employees visually. This reduces errors, increases productivity and also significantly shortens the familiarisation period.
AssisTable also offers a digital work catalogue that documents all work processes and improves quality assurance.
- Error reduction through digital support
- Visual instructions directly on the work surface
- Documentation and quality assurance through digital work catalogues
Automation and robotics
Automation and robotics can take over repetitive tasks and thus increase efficiency in production. Robots can work precisely and quickly. This improves the quality of the products.
When it comes to workplace optimisation in production, the integration of robots into production processes reduces the physical strain on employees and allows them to focus on value-adding activities. This is particularly relevant in logistics, where lifting systems automatically lift and lower heavy loads.
Lifting systems from Rocholz
The lifting systems from Rocholz have been specially developed for logistics. They lift and lower heavy loads (up to 60 kg) effortlessly and take the strain off employees.
Process optimisation and material flow
Lean production and Six Sigma are proven methods for process optimisation. They help to minimise waste and maximise efficiency. An optimised material flow is also crucial.
Good planning and organisation of the material flow ensure that materials are in the right place at the right time when optimising the production workplace. Methods such as Kanban systems and just-in-time (JIT) enable efficient material provision and help to reduce storage costs.
Lean Production and Six Sigma
Lean production aims to make all processes lean and efficient by eliminating waste and optimising the flow of materials. Six Sigma complements this approach by using statistical methods to improve processes and reduce error rates.
Both methods together ensure continuous improvement of production processes. This leads to higher productivity and better utilisation of resources.
Material flow optimisation
A well-planned material flow is crucial for the efficiency of workplace optimisation in production. Materials should always be available in the right quantity and at the right time.
Kanban systems and just-in-time (JIT) are proven methods for controlling the flow of materials and minimising stock levels. These systems help to avoid production interruptions and shorten throughput times. This is particularly important in flow assembly, where a smooth supply of materials is crucial.
- Kanban systems and just-in-time to control the material flow
- Minimisation of stock levels and production interruptions
- Improving throughput times in flow assembly
Use of conveyor technology
Conveyor technology such as roller conveyors and transport trolleys facilitate the flow of materials between workstations. Modular transport trolleys can be individually adapted to optimise production workstations and quickly modified as required. This increases flexibility and efficiency in the provision of materials and reduces the physical strain on employees.
An interesting and particularly space-saving system that fulfils these requirements is the solution from our partner Quick MOVE. This is an innovative 3D conveyor system for internal goods transport that enables flexible routing and leads to considerable space savings.
Safety aspects and quality assurance
Risk assessments and safety measures are indispensable components of workplace optimisation in production. Systems such as InspecTable recognise deviations and errors at an early stage and ensure high product quality.
Compliance with quality standards is ensured through visual inspections and continuous monitoring. In this way, companies can ensure that their products meet the highest standards.
Risk assessments and safety measures
Regular risk assessments allow potential risks in the workplace to be recognised and eliminated at an early stage. Safety measures such as protective clothing, emergency plans and regular employee training help to optimise your production workplace, prevent accidents and protect the health of the workforce. Ergonomic aids such as lifting systems and hoists minimise the risk of accidents at work.
Quality assurance systems
Quality assurance systems such as InspecTable use machine learning to recognise deviations from target values at an early stage. Visual inspections and continuous monitoring ensure that products meet the specified quality standards.
This reduces the error rate and improves customer satisfaction. The documentation and traceability of production steps also play an important role in quality assurance.
Training courses on occupational safety
Regular training on occupational safety and the correct handling of machines and equipment is essential. They increase employees' awareness of potential hazards (such as one-sided strain) and train them in the safe handling of work equipment. In the long term, this helps to reduce accidents at work and increases safety in the workplace.
Note: Regular training and quality assurance systems are essential for safety and quality in production.
Implementation strategies for continuous improvement
Gradual implementation of measures to optimise the production workplace is recommended. Start with pilot projects to test the effectiveness of the measures. Collect data and adapt the strategies if necessary.
Regular monitoring and feedback from employees are crucial to ensure long-term success. The use of change management methods can also be helpful in increasing employee acceptance of the changes.
Continuous improvement
Continuous improvement is an essential part of workplace optimisation in your production. Inefficient workflows can be identified and improved by regularly reviewing and adapting processes. This helps to increase efficiency and continuously improve working conditions.
Conclusion
Workplace optimisation in production is an ongoing process. It requires extensive planning and continuous adjustments. Ergonomic workplace design, technological support, process optimisation, safety measures and effective project management are central components of this process.
By implementing these measures for workplace optimisation in production, companies can increase efficiency in the long term. They improve product quality, promote the health of their employees and can reduce costs.